Our first set of tests characterizes the torque vs. preload relationship for each bolt. Why is this important? Let’s start with the purpose of torquing a bolt – it is to introduce enough clamping load (preload) into the bolt to keep the two bolted parts properly compressed during use. Too much preload, and the bolt may yield or break; too little preload, and the bolt may loosen or allow gapping in the joint.
Ideally, structural analysis would tell us how much preload is needed at each bolt location. With that information, we would measure the actual preload as the bolt is tightened until the desired value is reached. However, this is not practical without special instrumentation, so in most cases we rely on specifying the installation torque, and relating that indirectly to the bolt preload. Equations are available to relate torque to preload, but they always rely on an estimate of the friction in the threads and under the bolt head. Many online torque vs. preload calculators assume a certain “nut factor” when performing the calculation, but these calculators can be 30-50% off unless backed up by testing of the actual materials and finishes. That’s the intent of our tests – to find the actual “nut factor” for the different LBJ bolts.
When it comes to the LBJ bolts, Toyota specifies different torque values for the ’96-00 models (59 ft-lbs) and ’01-02 models (37 ft-lbs) (Figure below). Since the ball joints and knuckles are identical for all model years, we have to assume that different torque is specified because either: 1) Toyota decided in 2001 that less preload is needed than they originally thought, or 2) Toyota determined that the ’01-02 bolts achieve the same preload with a lower torque value than the ’96-00 bolts. Given that the ’96-00 bolts are flanged, and the ’01-02 bolts are hex bolts with washers, the latter is a plausible argument (flanged bolts may have more friction losses under the head). But there is only one to find out, and that is the purpose of this series of tests.
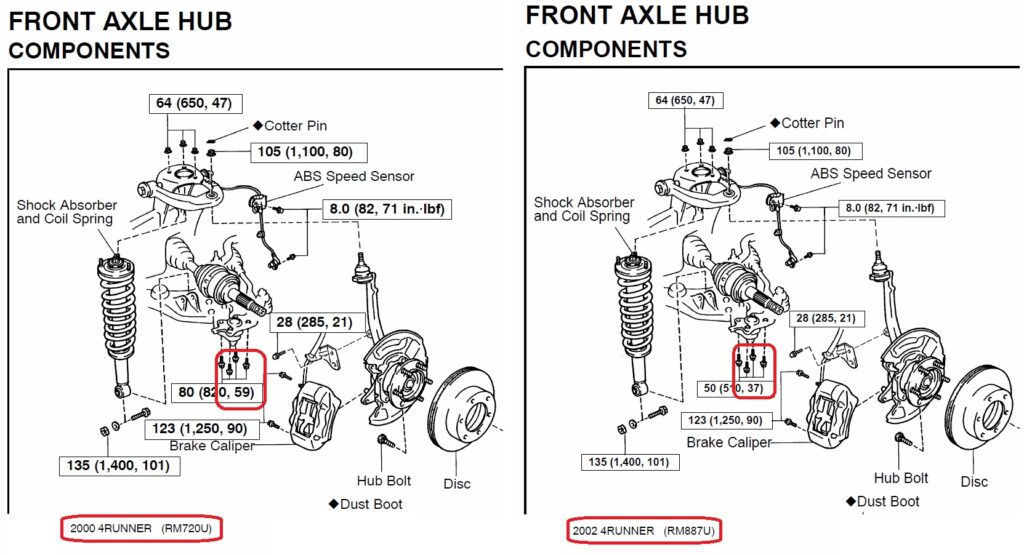
Test Setup and Process
In this first series of tests, we measure the torque vs. preload relationship for each of the five LBJ bolt types, to see if there is a significant (or any) difference, and if some bolts are more “slippery” than others, warranting a lower or higher installation torque value to reach the required preload.
For the tests, each bolt is inserted through a 1/4″ thick stainless steel bar (to provide a contact surface under the bolt head similar to the LBJ flange), then through a 10K lbs load cell, and threaded into a 7/16″ thick stainless steel bar, drilled and tapped for 10×1.25 threads. The load cell is connected to a digital multi meter to provide a direct indication of the load in the bolt. The bolts are torqued with a ratchet wrench, equipped with a torque transducer to accurately read out the applied torque. With this method, we can simultaneously measure the applied torque and the resulting preload in the bolt.
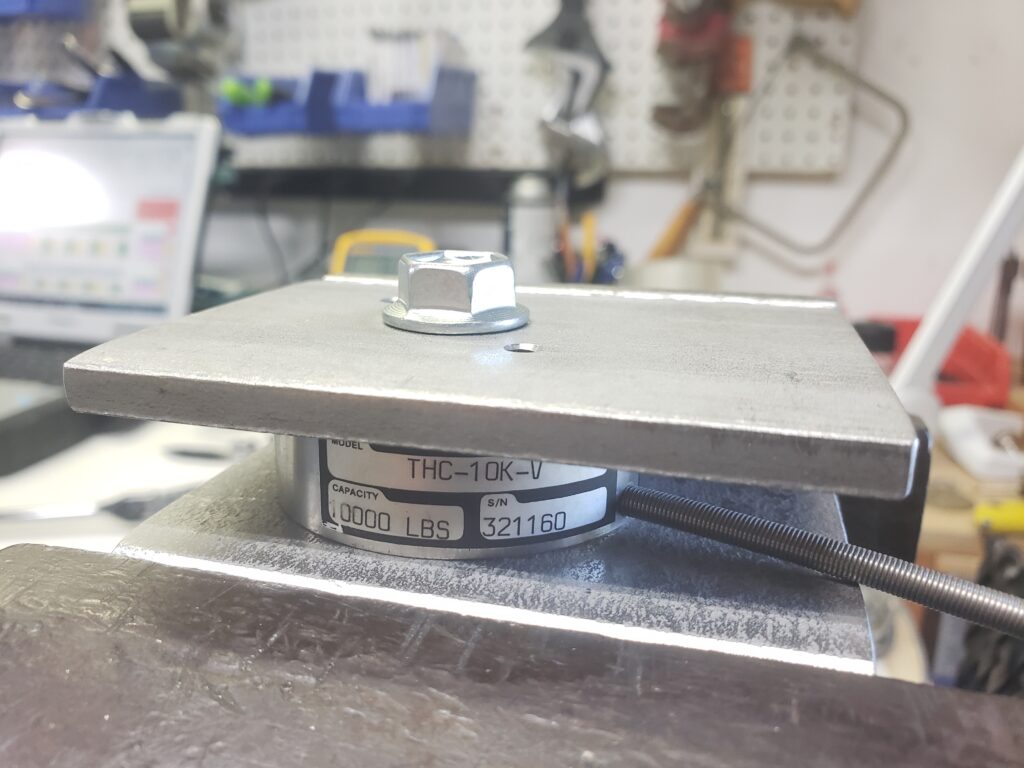
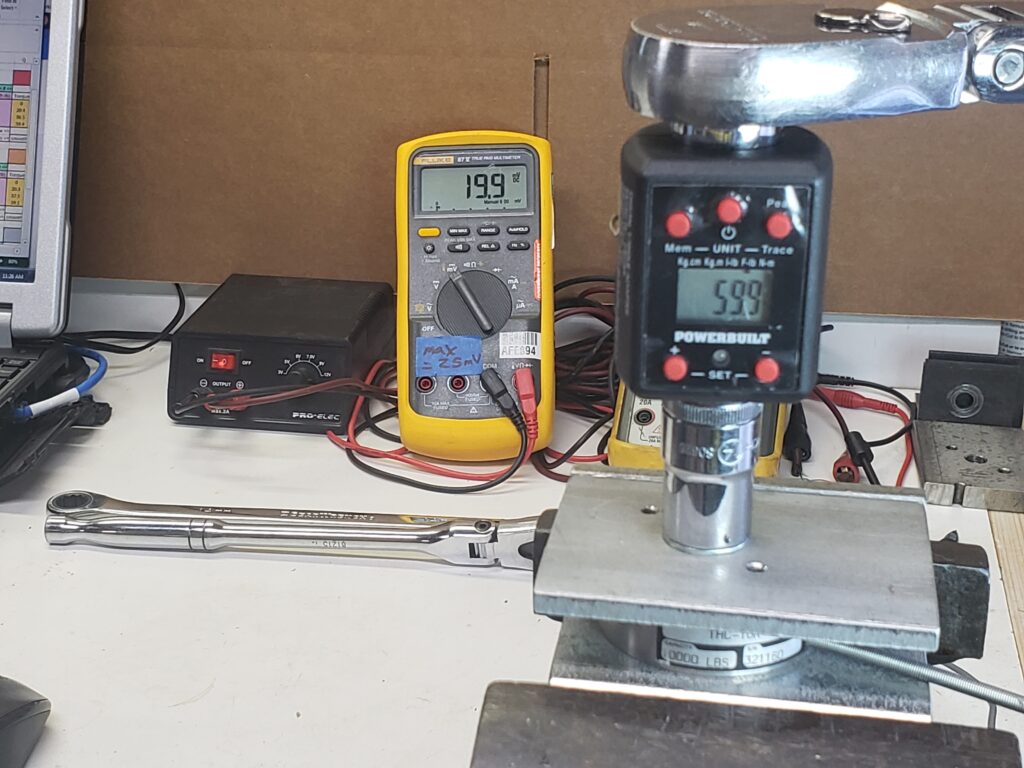
We torque each bolt to 20, 37 and 59 ft-lbs, and measure the load at each torque level. This process is repeated for three bolts of each type to account for unit to unit variability, and the results are then averaged to obtain the best fit torque to preload relationship for the bolt. We then repeat the process three times for each bolt, to measure how much preload at installation torque degrades due to reuse.
Results
First, here is the plot of torque vs preload for a brand new bolt of each type. This plot shows the average preload value generated by the three bolts for a given torque, on the first installation.
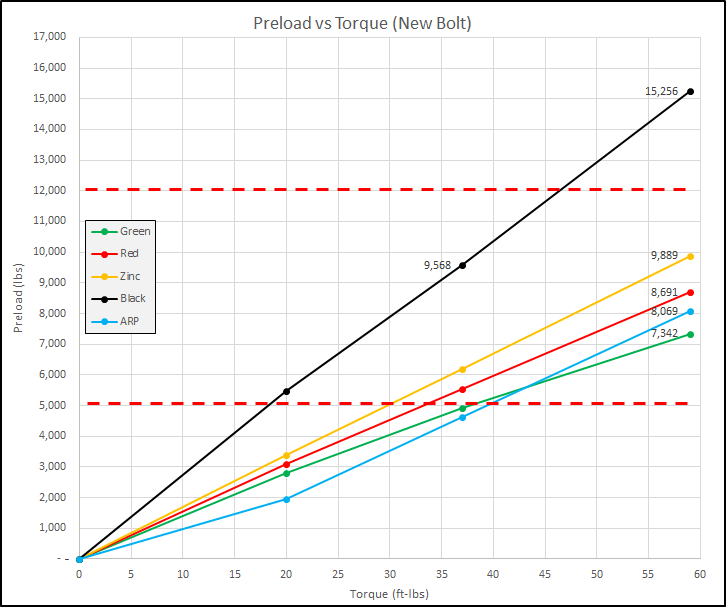
One thing jumps out right away – the Black bolt (aka “Bolt with Washer”, 90119-10933), generates a lot more preload at any torque value than all the other bolts. At 59 ft-lbs, it would generate around 15,000 lbs, which is higher than the safe limit for these bolts (we drew a red dashed line at 12,000 lbs as the upper limit for now, but we will confirm this later, during the destructive tests).
This chart also explains why Toyota specified a torque of 37 ft-lbs for the Black bolts, as opposed to 59 ft-lbs for the others – it’s not that the bolt is weaker, as some have speculated, but that it reaches the same preload (or higher) at 37 ft-lbs as other bolts do at 59 ft-lbs. So, conclusion number 1 – if you use the Black bolt, do NOT torque it to 59 ft-lbs, you will yield the bolt. Torque it 37 ft-lbs, as specified by Toyota.
The variation between all the other bolts is smaller, but still significant. The Zinc plated 10.9 bolt has about 10% more preload at 59 ft-lbs than the updated OEM LBJ Red bolt (90105-10505). The original OEM LBJ Green bolt (90080-10066) generates only 75% of the preload that the Zinc bolt does.
Using our spreadsheet for estimating torque to preload ratio as a function of bolt geometry and friction coefficient, the data above suggests that the friction coefficient is about 0.15 to 0.2 for all the bolts except Black; the Black bolt friction coefficient is likely below 0.1. That puts it squarely into dry film coating territory, which is pretty sophisticated for an automotive bolt application.
We tried to reverse engineer Toyota’s design intent, although of course these are just assumptions. The original Green bolt generates about 7,300 lbs at the specified 59 ft-lbs torque, while the updated Red bolt generates closer to 8,700 lbs. So we’re assuming that Toyota thought the 7,300 lb preload was a bit low, and in 2001 changed to the Red bolt with a different coating material, to bump the preload up to over 8,000 lbs. That is also consistent with the Black bolt, which generates over 9,000 lbs at its specified torque of 37 ft-lbs. So from this, we took the liberty to assume that the lower safe limit for these installations is around 5,000 lbs (it may be closer to 6,000 or 7,000 lbs for all we know). That lower limit is represented by the lower dashed red line in the chart.
Preload Degradation with Reuse
We ran additional tests to see how preload changes with repeated usage. It is often speculated on the forums that the LBJ bolts should only be used once, sometimes with the argument that the bolts yield during installation and thus should not be reused. Our data refutes that suggestion – 7,300 to 8,700 lbs at 59 ft-lbs for the flanged OEM bolts, and 9,500 lbs at 37 ft-lbs for the Black bolt is nowhere near the yield point. So from that standpoint, the bolts can be safely reused, unless you torque the Black bolt to 59 ft-lbs, which is guaranteed to yield it.
But the other concern with reusing a bolt is the reduction in preload with repeated cycles, due to wear. The chart below shows the percent reduction in preload as a function of repeated cycles, starting with a brand new bolt, and torquing it four times:
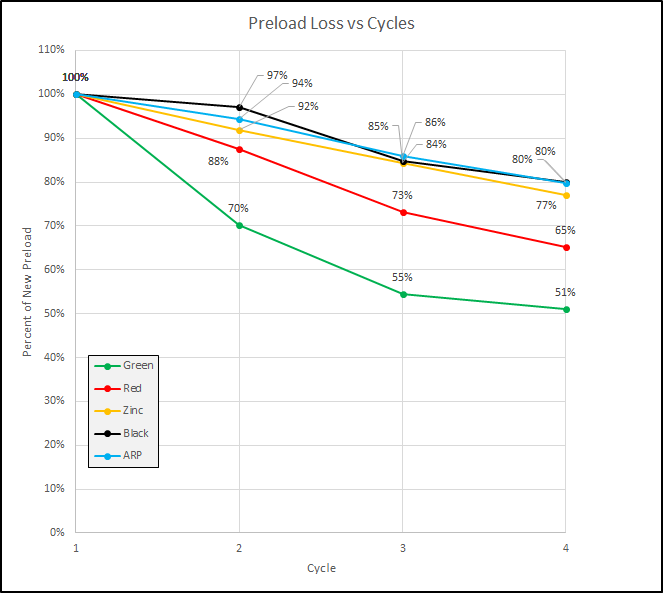
Three of the bolts (Black, Zinc, and ARP) maintain above 90% of original preload after the first cycle. Interesting to note that the two OEM flanged bolts (Red and Green) do not, they drop below 90% and 80%, respectively. By the fourth installation, the Green bolt has only half the preload of the first installation. The Black and ARP bolts still maintain 80% of original preload even after four installations.
The wide flange of the flange bolts (left photo) degrades significantly with installation cycles (new on left, four cycles on right). Compare that to the wear on the Black bolt (right photo), which is almost imperceptible. The low wear on the Black bolt also supports the conclusion that it has a dry film coating applied:
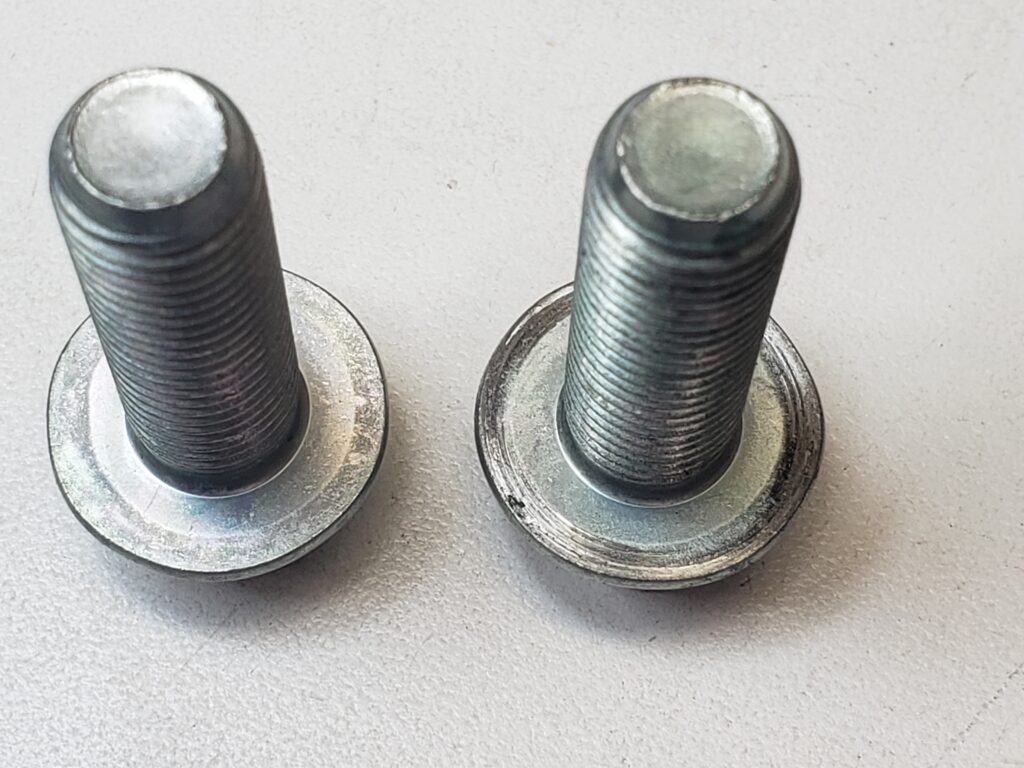
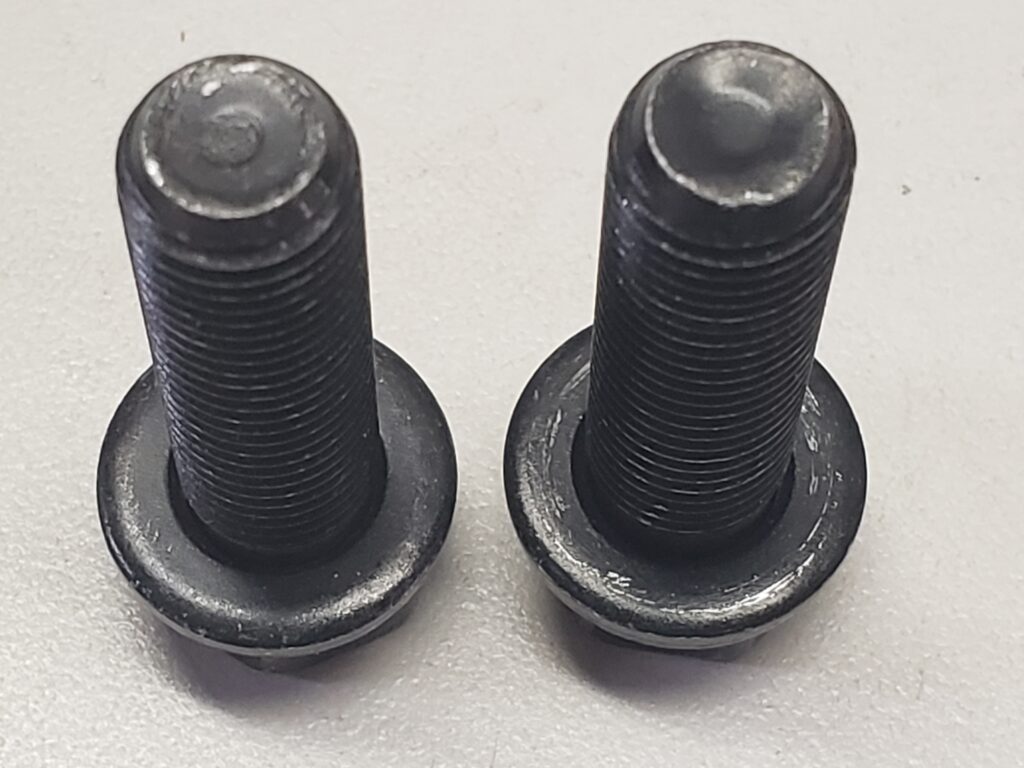
Below is a more useful way to process this data, looking at the actual preload as a function of installation cycles. This plot shows the preload achieved at 59 ft-lbs for the first cycle, as well as for three subsequent reuses. The Black bolt line is only for reference, as we should not torque it to 59 ft-lbs; the dashed black line at 37 ft-lbs is a better representation. Now we can see the effect of repeated installations on preload. In the worst example, the Green bolt drops to our assumed lower safe limit of 5,000 lbs with just one reuse. Additional cycles get the bolt to only about 4,000 lbs of preload.
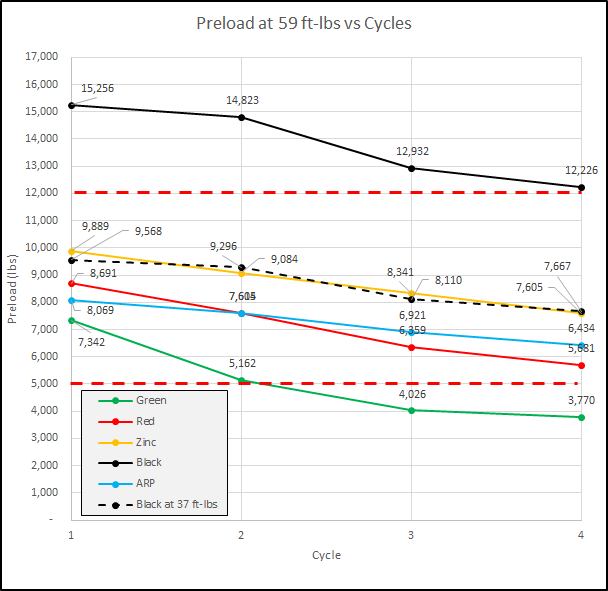
Conclusions
So how much preload do we need to not yield the bolts, and to not allow gapping during use? And how much torque should be applied to achieve that desired preload?
We can answer some of these questions using this data. Any of the bolts tested, when torqued to 37 ft-lbs for Black, and 59 ft-lbs for all others, will generate the needed preload on the first installation cycle without damage (7,000 to 10,000 lbs). Don’t torque the Black bolt to 59 ft-lbs, and don’t torque the other bolts to 37 ft-lbs, and you should be fine.
As for the low end, we think that most LBJ bolt failures occur due to insufficient preload, which allows gapping. This subsequently allows movement between the LBJ and the knuckle, likely leading to bolt loosening and breakage. Unfortunately we don’t know the lower preload limit at which gapping can occur. Our suspicion still is that 5,000-7,000 lbs is the low safe limit (especially for offroading), based on the fact that Toyota changed the bolt design to bump the nominal preload up from 7,300 to 8,700 lbs.
If you are going to reuse the bolts, especially more than once, we would recommend doing that only with the Black, ARP, or Zinc bolts. The two flanged OEM bolts simply have too much degradation after a few cycles. You could try to compensate for the preload degradation by bumping up the installation torque level, but without a load cell you will be doing guesswork (although with this data, it would be educated guesswork).
There is one other element that is not reflected in this data, and that is “feel”. As we torqued these bolts, the difference between the Black bolt and all the others (but especially Green and Red) was incredible. The Black bolt was smooth as silk – it rotated effortlessly, reaching the torque wrench’s click point easily (likely because it is dry-film lubricated). In contrast, the flanged bolts, especially on repeated cycles, bucked during torquing, leading to jerky stick-slip type of motion. The clicking of the torque wrench was not nearly as pronounced as with the Black bolt.
1 thought on “LBJ Bolts Preload vs. Torque Tests”
Thanks for a thorough testing of the different LBJ bolts. Will use pre-load and torque data when doing LBJs next time.
Comments are closed.