Taking the data collected in our previous tests, we ranked the bolts to find the winners and the losers. We first defined what we consider to be the important criteria for LBJ bolts, then assigned different weighting factors to each criteria. For example, criteria that improved confidence in knowing the actual preload generated at FSM torque was weighted more heavily than secondary criteria such as preload degradation with reuse. We then scored the bolts against these criteria using their measured performance, and added up the scores to get the total combined score for each bolt.
Using this admittedly subjective criteria, the combined scores for all bolts are in the figure below. The winners are the Black Bolt (90119-10933) and the ARP Bolt (673-1004). The Red and Green bolts were also good, but not as good the Black and ARP bolts. The 10.9 Zinc bolt was far back in last place.
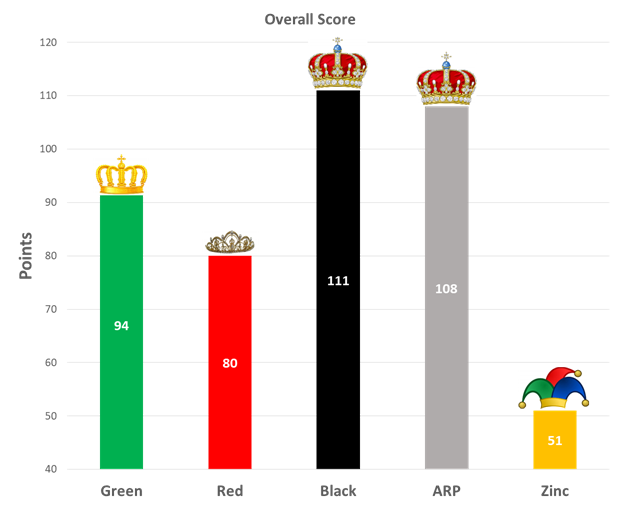
Based on these results, our top recommendation for LBJ bolts would be the Toyota Black Bolt w/Washer (90119-10933) or the ARP Bolt (673-1004). The Black bolt excels in its incredibly low friction coefficient, which leads to a silk-smooth installation, and allows the bolt to reach 10,000 lb of preload at only 37 ft-lbs, significantly higher than many other bolts could achieve at 59 ft-lbs. It also provides the highest confidence in the preload generated at the applied torque, and does not have much degradation with reuse. The ARP bolt is the strongest of the group, giving it very high margin between installed torque and yield torque. It also does not degrade much with reuse.
The Red and Green bolts are certainly adequate for LBJ use, although they don’t have as much margin between installed torque and yield torque as some others. They also have the highest degradation with reuse, so we would not recommend reusing these bolts more than once. By the third or fourth installation, you would likely be seeing only half the preload at the FSM torque as you would during the first installation.
The 10.9 Zinc bolt fared far worse than all others, primarily due to its very high friction variability from unit to unit and batch to batch. Without testing each batch like we did, you would have no idea how much preload is being generated at the FSM torque. For this reason, we would recommend avoiding any generic bolts for the LBJs.
There is one caveat about the Black bolt that must be mentioned. This bolt was designed to be torqued to 37 ft-lbs, due to its very low friction coefficient. The downside of this is that if these bolts are torqued to the more commonly quoted FSM torque of 59 ft-lbs, they will likely yield. We’ve seen many forum posts where folks have torqued the Black bolts to 59 ft-lbs and had them break, then concluded (wrongly) that the Black bolts must be weaker than others. So the caveat is that if these Black bolts are installed in trucks that originally came with Red or Green bolts, anyone working on these trucks in the future must be told to torque the bolts to the lower torque values. This is particularly important if you let a mechanic work on your truck, who may not be aware that you installed non-factory bolts with lower torque requirements.
A Remaining Concern for LBJ Bolt Failures.
An important element that these tests did not address is the possibility of LBJ bolts losing preload and backing out, especially during offroad use. We believe that this is the most common failure cause for LBJ bolts, because properly preloaded bolts will rarely fail or shear off (the friction generated by four preloaded LBJ bolts is quite high, and there are two large shear cones on the LBJ that engage the steering knuckle to resist the shear loads).
However, if the bolts lose preload, they are more likely to loosen and eventually fall out. We’ve seen a number of posts with folks finding one or more missing bolts in the LBJs, suggesting that torque alone may not adequate to keep these bolts safely in place during offroad use. Even if the bolts don’t fall out, loss of preload will subject the joint to gapping and slipping, and the bolts will become more likely to fail from bending loads.
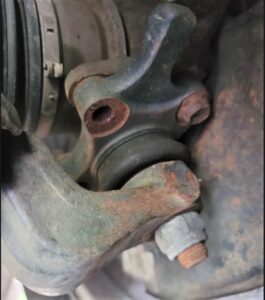
A common practice to address this risk is to use Loctite or a similar threadlocking compound. While these are effective if used properly, there are two concerns – first, there is no way to know if the Loctite was applied properly and has formed an effective bond. In addition, it is not possible to look at an installed bolt and know if Loctite was applied to it during installation. The biggest issue with Loctite is that it affects the preload that is generated during installation. While it does not change the preload very much during the first installation, our testing found that on reuse, even if the bolt threads were carefully cleaned with a wire wheel, the preload ended up being much lower than on initial installation. The most likely explanation for this is that cured Loctite remained in the female threads of the knuckle, increasing the friction coefficient. So unless the threads are chased with a tap after each use, there is likely to be much less preload in the joint than intended or desired.
Even the “best” bolts will be of no value if they loosen in use. So we believe that properly “locking” the LBJ bolts to keep them from loosening is as critical as selecting the “best” bolts, if not more so. How to achieve this effective locking is a whole separate discussion.
Detailed Scoring Criteria
Preload Uncertainty – This criteria ranks the uncertainty in preload generated by a bolt when it is torqued to FSM torque (or any other value). The narrower the range, the less uncertainty in the preload, and the higher the score.
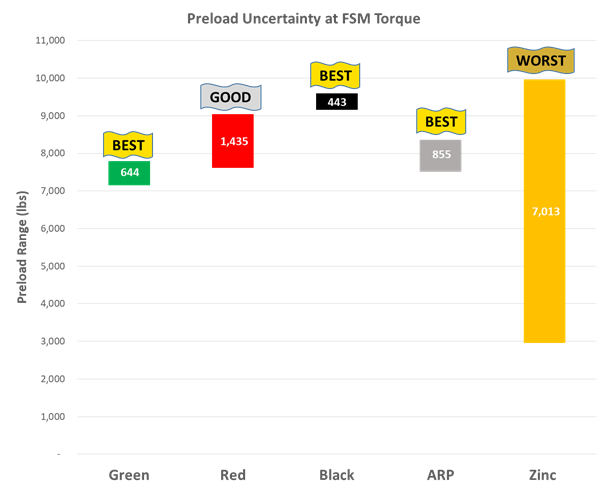
Bolt Strength – It stands to reason that all else being equal, the stronger the bolt, the better. Stronger bolts can be preloaded to higher clamping loads, providing higher margins against slipping and gapping.
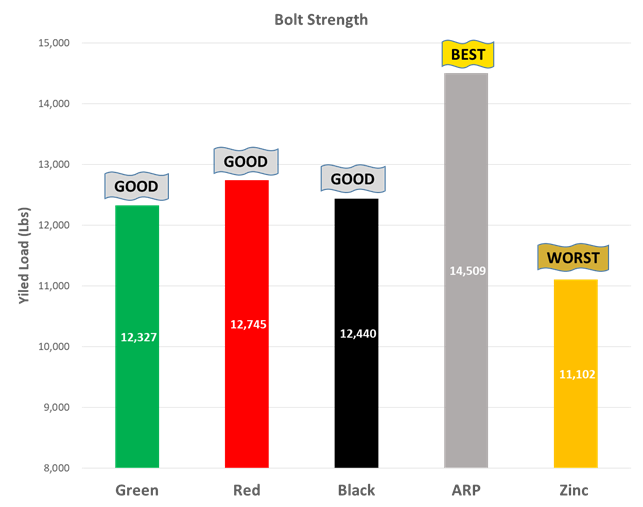
Preload at FSM Torque – Some bolts reached much higher preloads than others at FSM torque values. Higher preload is better, as it reduces the chance of gapping or slipping.
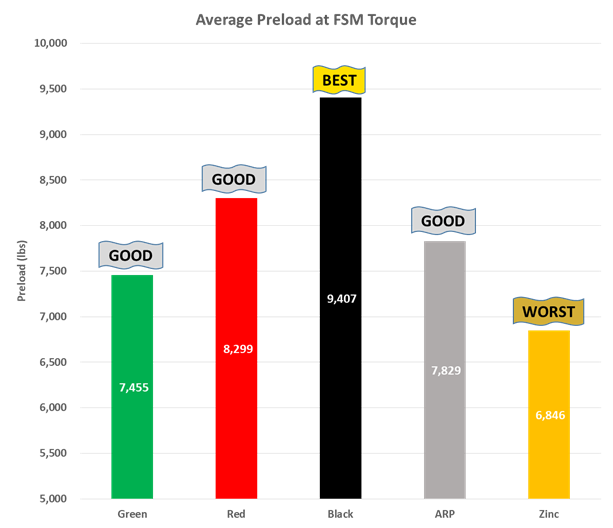
Margin between FSM torque and Yield Torque – This criteria evaluates how much safety margin exists between the FSM torque and the torque at which the bolts fail (yield). The higher the margin, the more room for error exists.
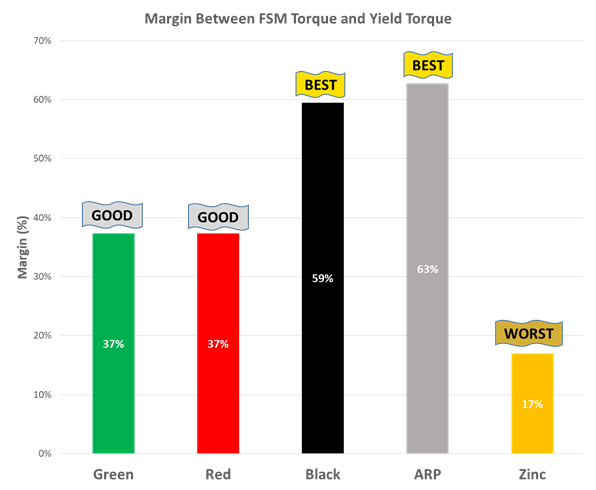
Preload Retention with Reuse – Some bolts saw a significant reduction in preload between first use and subsequent installations; others did not. Since the LBJ bolts are commonly removed to separate the knuckle from the lower control arm, the ability to reuse the bolts with high confidence would favor those bolts that perform consistently during repeated installations.
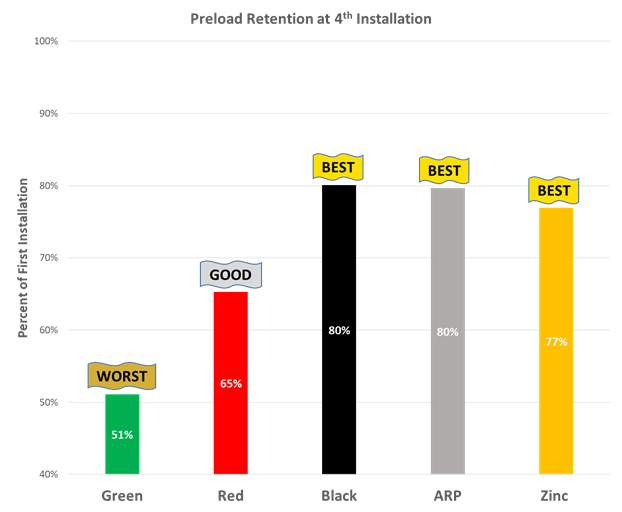
Friction Coefficient – This criteria has little practical value other than “feel”. The bolts with low friction coefficient felt very smooth during installation, and reached the FSM torque values easily. The ones with higher friction, notably the Zinc bolts, were jerky and had significant stick-slip during installation, making the torquing process more difficult.
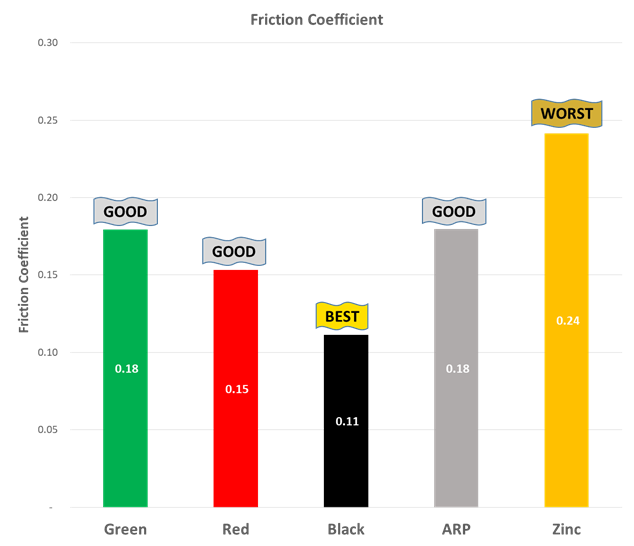